Connectivity for the Next Generation of Field Service Management
EquipConnect provides real-time equipment data essential for proactive and predictive measures that sustain maximum uptime.
EquipConnect unlocks legacy and modern equipment data, providing secure Internet of Things (IoT) connectivity. It empowers businesses with remote capabilities, such as fault conditions alarms, diagnostics, equipment settings control, and triggers work-order notifications directly to FieldEquip. Furthermore, FieldEquip’s edge gateway technology can decipher complex data streams from traditional log files and IoT sensors or tap directly into PLC data through a local machine network.
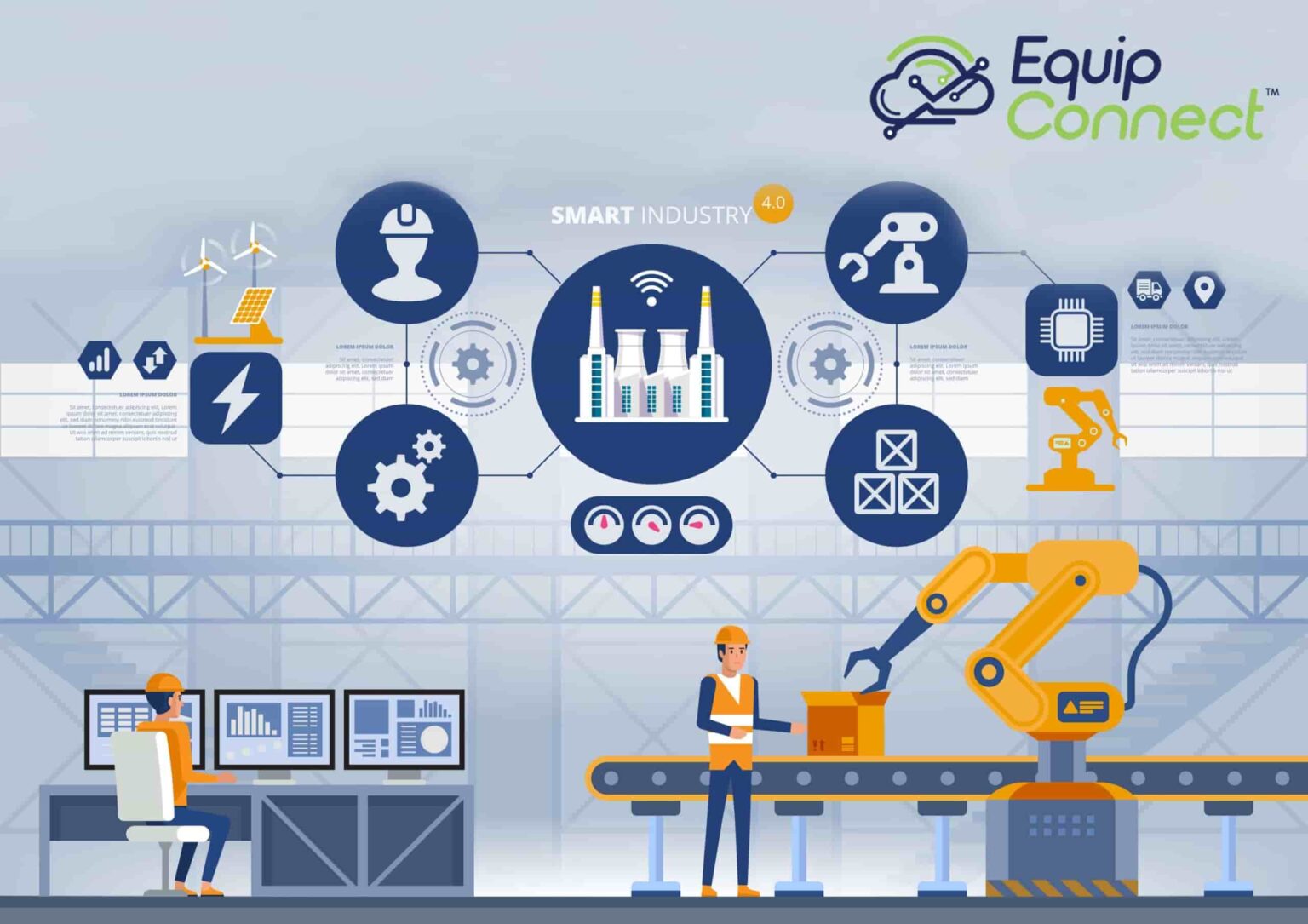